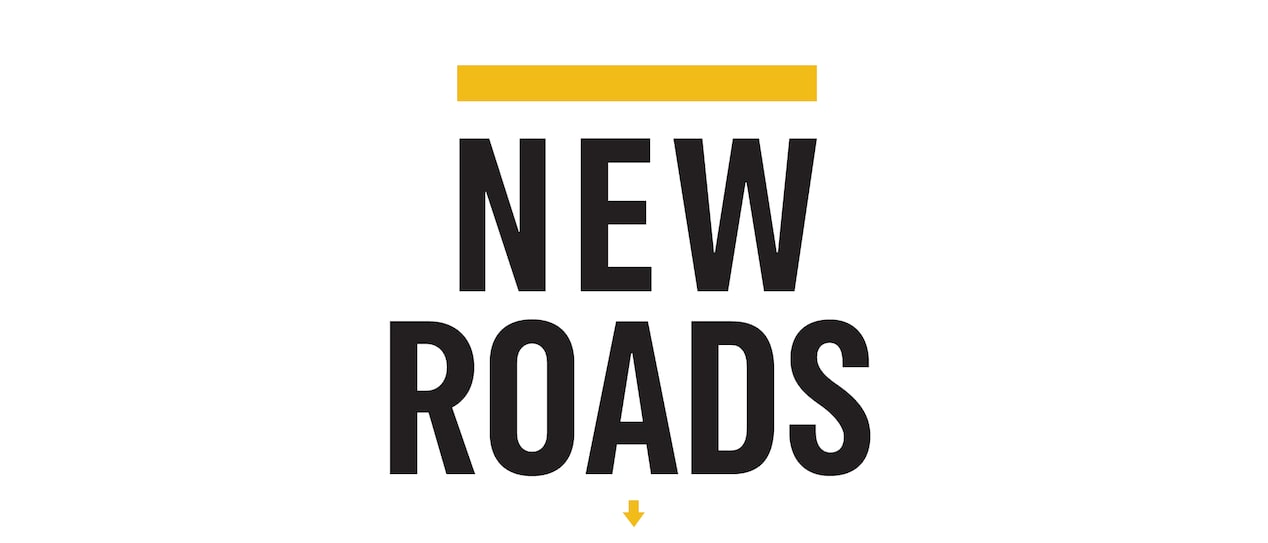
Stories for people
Who want to discover more
New Roads is devoted to all of us who seek out interesting paths and possibilities—purposefully, confidently. Enjoy exclusive previews of new vehicles, behind-the-scenes looks at cutting-edge technology, and profiles of Chevrolet owners getting the most from their vehicle and the places it takes them.
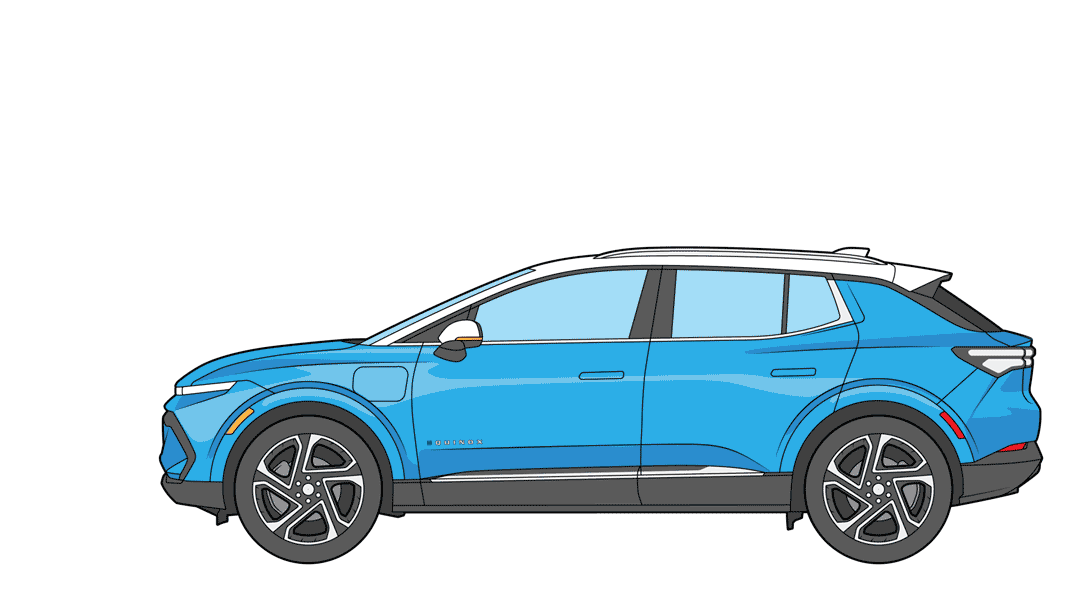
Capturing EV Energy One Breath at a Time
Engineers are developing surprising ways to capture and use excess energy in Chevy's new electric vehicles to help drivers make the most out of every mile.

Designed from the Ground Up
The evolution of Chevrolet’s electric vehicles began with these designers and engineers, who tell the story of how they started from scratch to create owner-focused EVs.
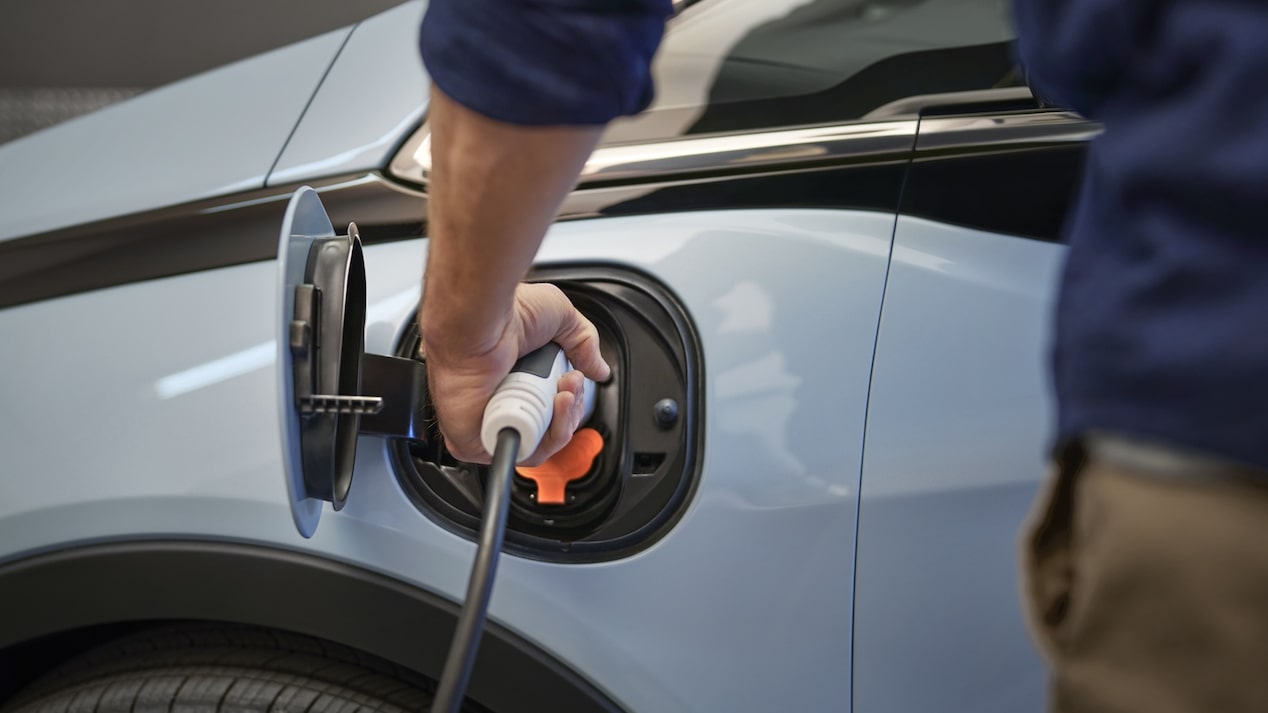
Taking Charge
For EV ownership to make sense for everyone, Chevy looked at how to help owners feel confident on the road. They started with a commitment to seamless charging at home or away.
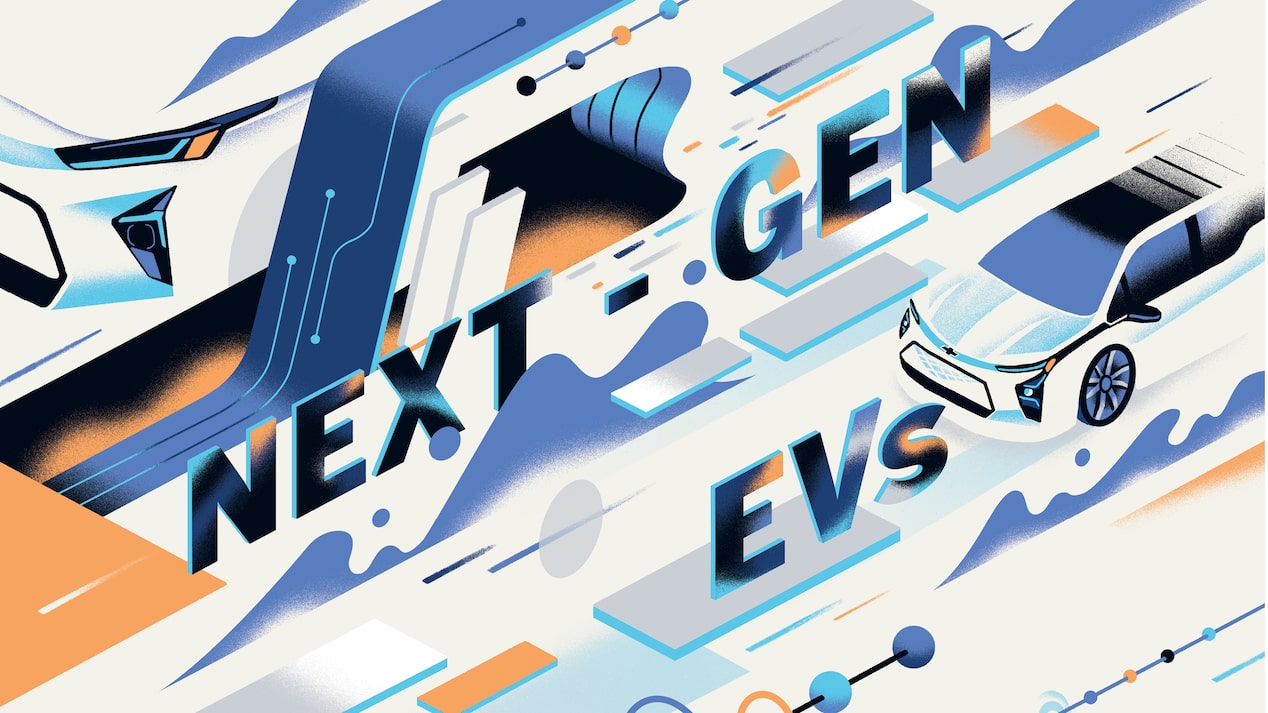
Next-Gen EVs
Chevrolet is gearing up for its electric future with the Ultium battery platform, bringing flexibility and innovation to a new generation of electric vehicles.
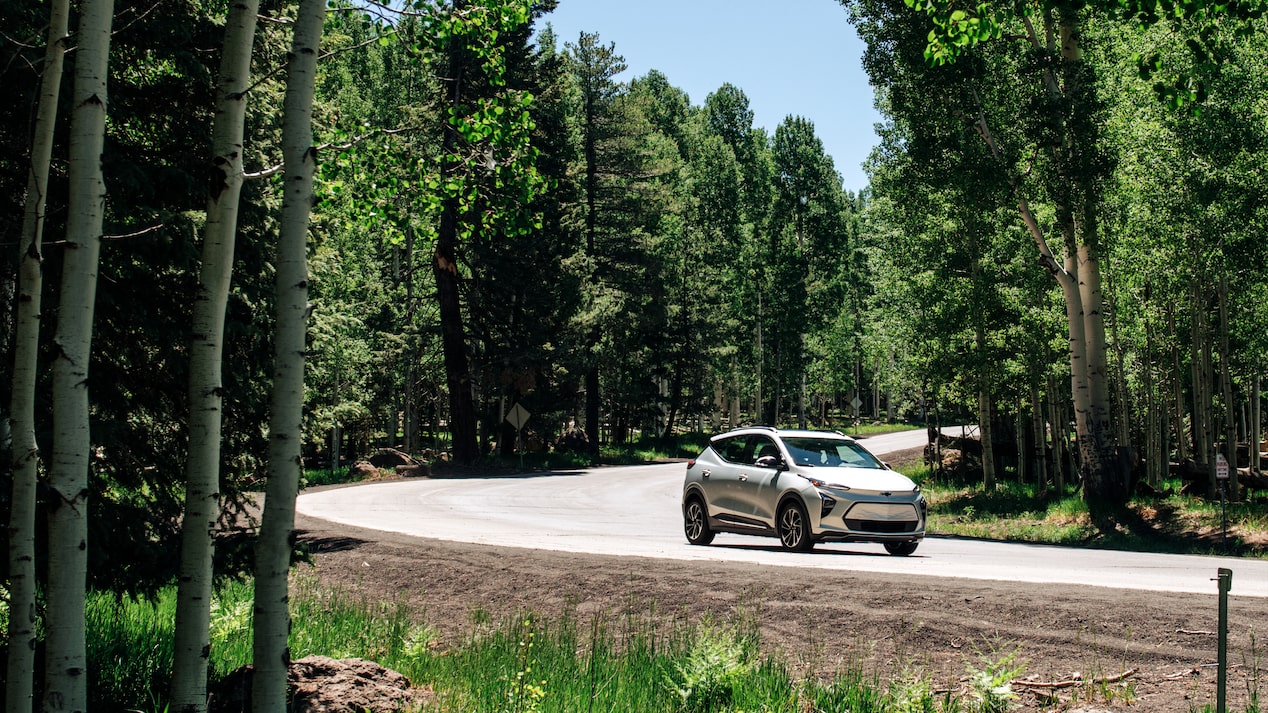
The Future Electric: Battery Technology
Kristen Siemen, chief sustainability officer at GM, delves into the future of the company's electric vehicles and the innovative path to reach it.
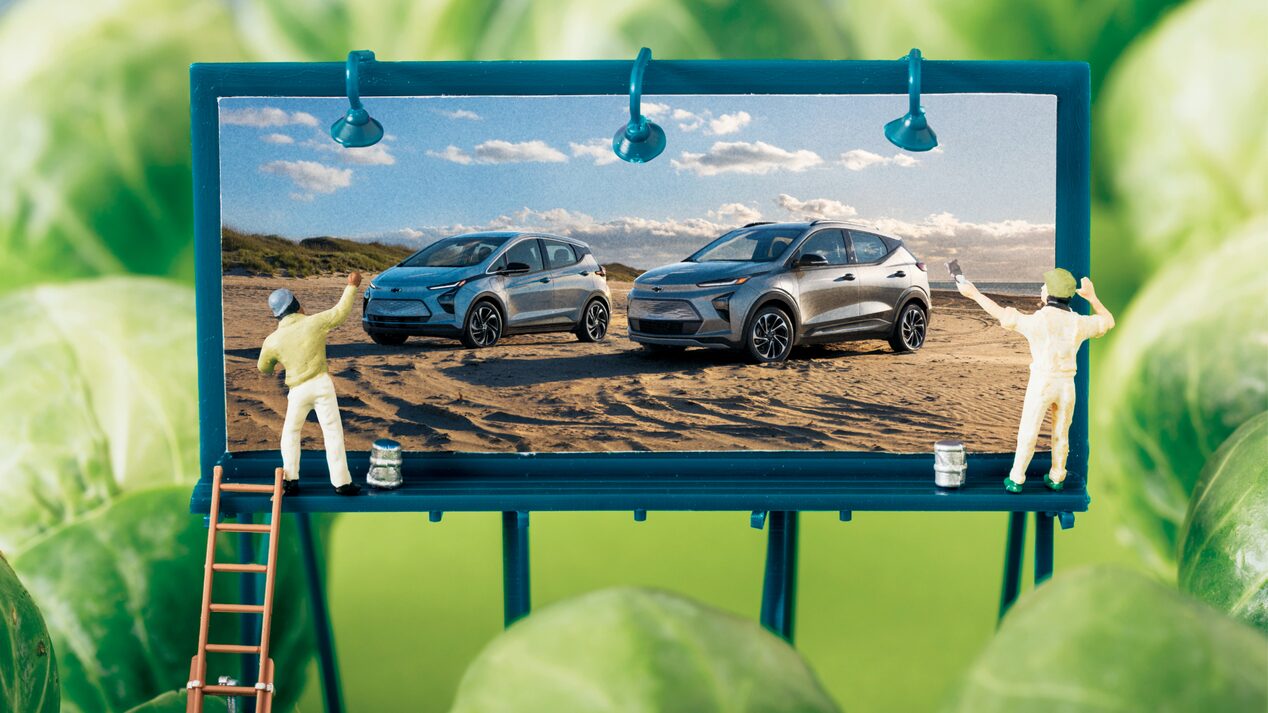
EV Myth Busting
It’s time for some facts and figures that bust outdated myths about electric vehicles. Take a closer look at how easily an EV can fit into your driving life.
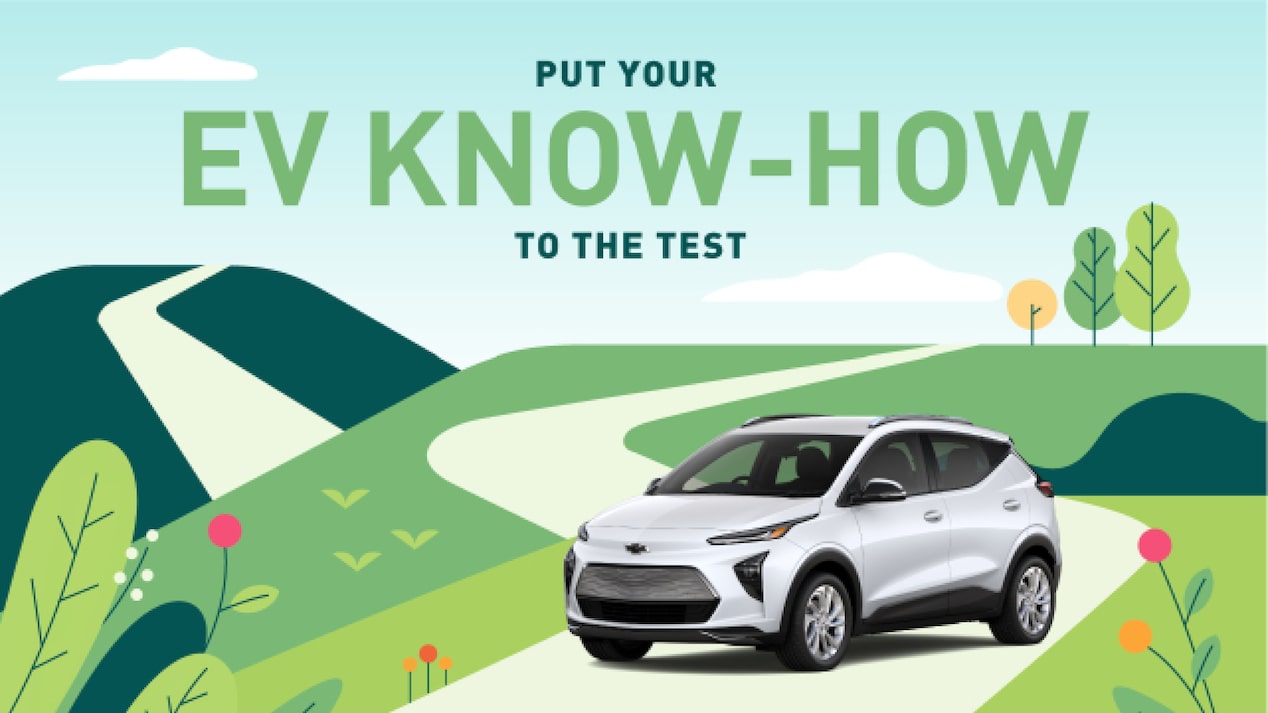
EV Academy
Before you unplug that charge cord and unleash electric torque out on the open highway, take our quiz to see how much you know about getting the most out of your Chevrolet electric vehicle.
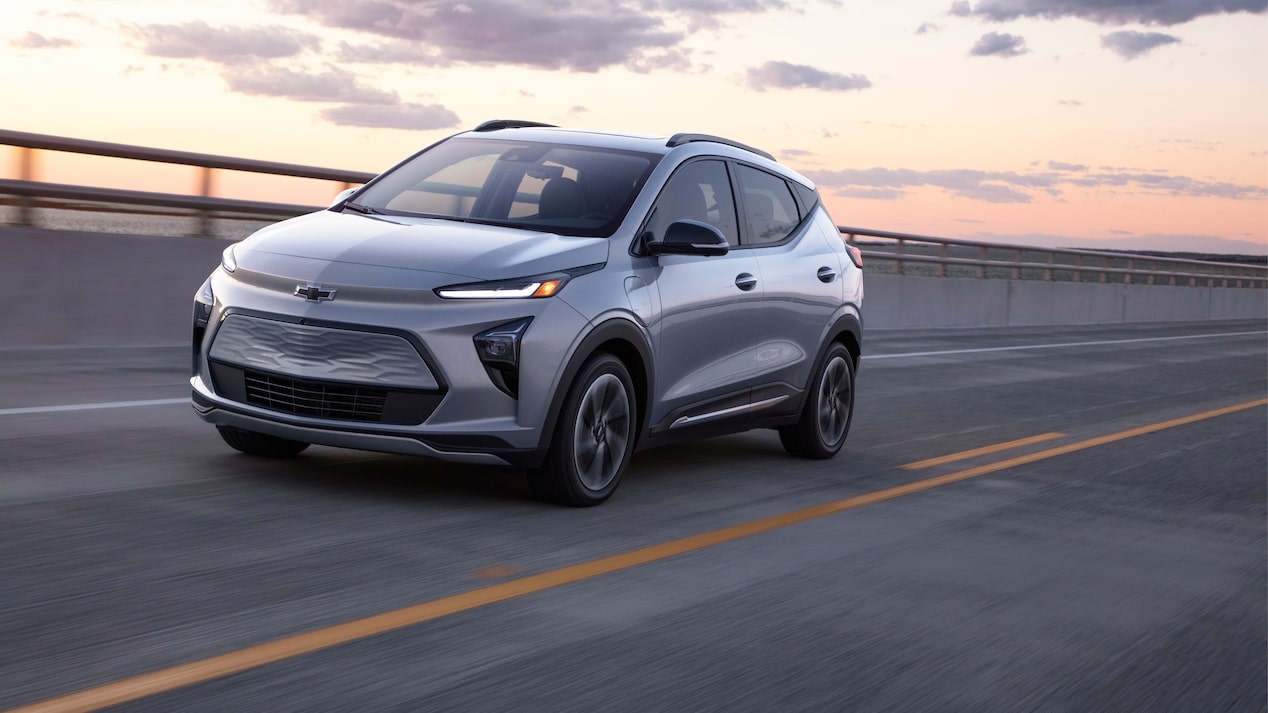
The Future Electric: Charging Infrastructure
Chevrolet has a vision for a charging infrastructure that will meet the needs of a future that sees widespread adoption of electric vehicles, and is working with Qmerit and EVgo to make it happen.